- No Obligations
- Stop Paying Too Much For Your Contractor
- No Spam Calling
- Screened & ID Checked Contractors only!
OSHA Standards Explained for Employees and Employers
1
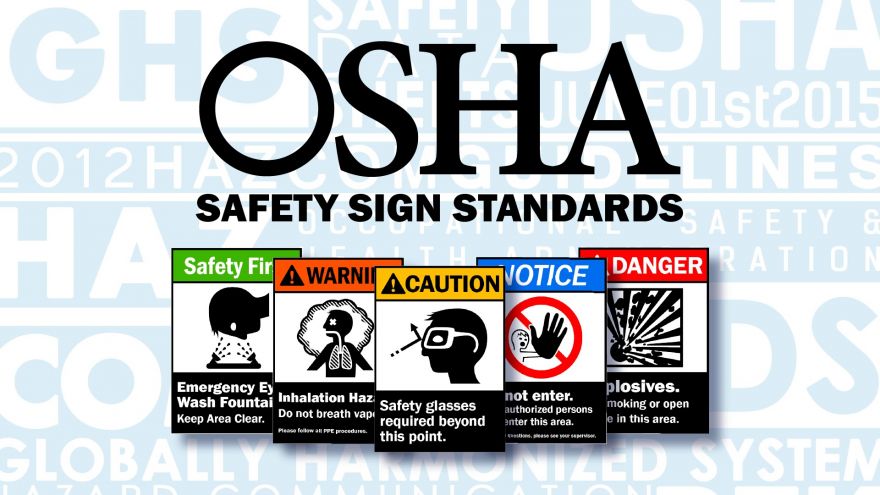
For almost fifty years, workers in the United States have had government protection in the workplace with the Occupational Safety and Health Act. Passed in 1970, the Act requires employers to provide a safe working environment for their staff. The Act also created the Occupational Safety and Health Administration (OHSA) which has the power to lay down standards for health and safety in the workplace.
Who Is Covered by the OSHA?
The Act covers most workers in the United States and its territories through the Federal OSHA program, or through OSHA-approved programs at the State level. These State-run programs must be at least the equivalent of that at the Federal OSHA level. The Federal OSHA standards and legislation generally cover workers in the private sector. State and local government workers are not covered by the Federal statutes and are looked after under the State schemes approved by the OSHA. Postal workers are the only Federal employees covered explicitly by the OSHA, others Federal government workers have agency-specific programs.
Who Is not Covered by the OSHA?
The bulk of people not covered by the OSHA legislation are self-employed. Also not covered are family members of farm employers, who don’t hire any other labor. If workers are protected by another Federal agency such as the FAA, the US Coast Guard, or the Mine Safety and Health Administration, they too are not covered by OSHA.
What are OSHA Standards?
The standards set down by the Occupational Safety and Health Administration are the method and rules by which employers must protect their workforce from hazards. The standards set down for general industry applies to most workplaces. There are also specific standards for construction and maritime work.
The standards laid down the safe practices that should be used in the workplace, and any safety equipment that should be provided. They also put a limit on a worker’s exposure to hazardous chemicals. It is a requirement of employers to monitor any hazards in the workplace and keep a record of any illnesses and accidents that arise. There is also a catchall in the legislation which means employers must conform to the general duty clause in the Occupation Safety and Health Act. The general clause makes it the responsibility of all employers to keep their workforce safe from any recognized hazards. If no specific OSHA standard applies, this is usually cited.
Employers Responsibility
All employers covered by the OSHAct have a statutory obligation to provide a safe workplace, what is free from dangerous hazards, and complies with OSHA safety and health standards. It is the duty of employers to identify and rectify any health and safety problems. The OSHA goes further in requiring employers to try to eliminate or reduce workplace hazards by altering the working conditions. It is not good enough to just supply protective equipment such as face masks, gloves or earplugs. Employers are duty bound to use the safest chemicals available and to make sure that any harmful fumes are properly ventilated.
✓ Employers must train their employees about the hazards in the workplace so that they can learn and understand any warning labels, alarms, coding, or information about harmful chemicals.
✓ Employers must keep precise records of work-related illnesses and injuries.
✓ Employers must do adequate testing in the workplace, such as sampling air for hazards, so the workplace meets OSHA standards.
✓ Employers must provide any medical tests necessary by OSHA standards.
✓ Employers must also display the details of any OSHA citations, along with illness and injury data, in the workplace so all staff can see them.
✓ Employers have a legal responsibility to inform the OSHA within eight hours of a death in the workplace, or an incident involving three or more workers.
✓Employers can not retaliate against any employee who uses their rights under the OSHAct, and the law in general.
Which OSHA standards are broken the most?
Every year the OSHA publishes a list of the top violations of its health and safety standards. The list reflects the incidents reported and investigated where a breach of the OSHA standards has occurred. Over the years, there has been little variation in the top ten standards violations.
Fall Protection – Construction: The OSHA has two types of fall protection standards, those in the construction industry, and another set for the general industry. The latest report shows that employers in the construction industry violated the Fall Protection Standard more than any other. Construction workers on a typical work site face many fall hazards. They have to work on ladders, roof, or steel beams and can fall down stairways or into holes. Workers can also fall into hazardous machinery. The OSHA standard expects employers to institute the necessary safeguards, so workers are unable to fall from elevated platforms and workstations or to drop into holes. Fall protection needs to be in place if an employee is working at least six feet above the ground.
Hazard Communication – This standard requires employers to make clear to every member of the workforce any hazards, particularly chemical, that may be present in the workplace. There must be adequate education on the dangers involved with any substances, and what workers must do to protect themselves. There must be enough training, so staff are sufficiently qualified to use or handle any dangerous chemicals.
Scaffolding – Every year, thousands of workers are killed or injured when working on scaffolding. Accidents occur when employees are erecting and dismantling scaffolding, and when getting on or off. The OSHA standard for scaffolding is particular to the construction industry. The aim is to protect workers from harm from things like falls, electrocution, a scaffolding collapse, or objects falling from the structures. Employers must make sure anyone working with or on scaffolding has the proper training, and that the standards are met for its erection, dismantling and use.
Breathing and respiratory protection – There are lots of workplaces in various industries where workers may be exposed to dust, vapor, gases, fumes or sprays. If these substances are inhaled, they can lead to lung diseases. If the exposure lasts a long time, the employees may suffer an occupational disease such as asbestosis or silicosis. The standard set down by the OSHA requires employers to create and enforce a program for respiratory protection. It is the duty of an employer to identify any airborne hazards and provides the correct safeguards and to make sure any safety equipment is maintained and in working order.
Tagout or Lockout -The OSHA has introduced standards for equipment that can store energy, and thus injure a worker even though it may be switched off. The idea is to prevent injuries such as to maintenance staff who might be working on a machine that has stored energy in its electrical system and can give an electric shock even though it is not connected to a power source. In these cases, the OSHA standard requires either a lockout device, which will stop the equipment operating or a tagout device which must be removed before any maintenance can be performed.
Ladders – Figures from the OSHA show that about a fifth of all injuries in the workplace involves the use of ladders. The OSHA standards suggest trying to eliminate ladders wherever possible, by designing projects so they can be done on the ground. If that is not practical, then using a safer alternative to a ladder is recommended, such as an aerial lift. If this is not doable, then an employer must make sure workers use the right type of ladder, and they have the right safety accessories to work on the ladder.
Powered Trucks – The OSHA estimates that one in ten forklifts are involved in an accident every year and that 100,000 workers are injured annually. These vehicles are described as powered industrial trucks by the OSHA. Employers in all industries are required by the OSHA to train workers how to properly operate a forklift or any other type of powered industrial truck. Workers who have been trained must be appropriately certified, and that operators much be recertified every three years.
Machine Guards – If a machine is cutting, punching, or shearing metal, wood or plastic the OSHA standards require the correct safety guards be in place. These machines with moving parts can seriously injure workers. There are a number of options available to employers to ensure machine operators are protected from hazards. Machinery can have fixed guards, safety trip controls, gating, or pressure sensors.
Protection from Falling – This is a more general standard for industries other than construction. Employers are obliged by the OSHA standard to provide training for workers who may be at risk of falling due to their working environment. They must be given the appropriate training to recognize a hazard and minimize the risk. If workers have English as a second language and do not understand it completely, the employer is obliged to provide the training in their native language. The employers also must keep a written record of who has been given the training and when.
Electrical Wiring – The OSHA standard to prevent electrocution, shocks, burns, and other injuries caused by faulty wiring is called Wiring Methods, Components and Equipment for General Use. Employers are required to make sure all electrical wiring is correctly grounded. The standards prohibit the use of flexible wiring, such as extension cords in a building to replace the fixed wiring. The electrical wiring standard is very technical, and along with most OSHA standards needs the assistance of a certified professional to implement correctly.